Чудеса из крошки резиновой
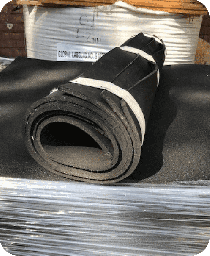
Ультра-, эко-, -вибро чудеса
Появление на рынке стройматериалов изделий именуемых антивибрационными и произведенных из резиновой крошки и полиуретанового клея немедленно вызвало вопросы у потребителей. А так ли все замечательно, как пишется в материалах от маркетологов компаний с названиями “Эко-…” и “Ультра-” и т.д.? Действительно ли такие материалы под привлекающими внимание названиями “Вибро-” и “… рез” являются вибродемпфирующими и даже аналогами, в т.ч. зарубежных, виброизоляционных материалов Sylomer, Sylodyne, Vibrofoam, Gener, Nowelle?
Из текстов на сайтах эко- и ультра- компаний можно прочесть, что виброрезы, как их теперь именуют, это смесь резиновой крошки, произведенной из автомобильных шин и олигомерной композиции на основе изоцианатов, т.е. реально это аналоги хорошо знакомых покрытий для детских площадок, но под другим — “виброизоляционным” именем.
Компании заявляют виброрезы инновационными высокотехнологичными продуктами с уникальным комплексом виброзащитных свойств, не обращая внимание клиента на то, что большая часть составляющих этих изделий — дробленые шины со свалки.
Из чего же, из чего же, из чего же сделаны...?
Для изготовления “антивибрационных” материалов берётся резиновая крошка, получаемая дроблением автомобильных покрышек, и такая крошка самая дешевая. А что представляет собой такая резина в составе этой крошке? Основа шинных резин — комбинация каучуков — натурального и синтетических изопренового, стирольного и дивинильного. Интересно что шинные каучуки, ввиду своего химического строения, характеризуются одним из самых высоких среди эластомеров показатель эластичности, т.е. имеют низкое внутреннее трение макромолекул, т.н. гистерезис. И это крайне важно для автомобильных шин, которые должны амортизировать удары, защищая таким образом подвеску машины. Но вот для демпфирования вибрационных колебаний они почти бесполезны.
Для настоящего вибродемпфирующего материала, в частности демпфирующей эластомерной пластины ПД-С-Ф-10-500х500 которая изготавливается по ТУ 22.19.20-133-75233153-2022, необходим высокий гистерезис, за счет чего, ввиду высокого внутреннего трения внутри полимера, есть бóльшая потеря механической энергии, что приводит к поглощению колебательной энергии. Такие характеристики можно достичь использованием эластомерных продуктов на базе синтетических бутадиен-нитрильных каучуков и полиизобутиленовых полимеров.
Что такое резиновая шинная крошка?
Химический состав резиновой крошки, из которой производят виброрез, зависит от вида сырья, из которого она изготовлена, т.е. от типа автомобильных шин (а они бывают зимние, летние, легковые, грузовые, КГШ и т.д.) и даже от той части той самой шины (протектор, боковина, борт и т.д.), который в процессе дробления превратился в крошку. А поскольку рецептуры резин упомянутых деталей автомобильной покрышки сильно разнятся, то и технические показатели видов резиновой крошки серьезно различаются. Но потребитель “антивибрационного” виброреза об этом редко догадывается, а им никто и не объясняет
В отличии от виброреза и их аналогичных изделий, у демпфирующих эластомерных пластин, таких как ПД-С-Ф, которые изначально разрабатывались для использования в качестве виброзащитных и виброгасящих материалов, состав всегда стабилен, поскольку в составе во-первых отсутствуют продукты вторичной переработки, а во-вторых применяются только первичные бутадиен-нитрильные каучуки. Поэтому технические характеристики, в том числе способность к поглощению энергии вибрационных колебаний, виброзащитных эластомеров от компании “Вулканикум” всегда стабильны.
“Подводные камни” от применения виброрезов
Наличие резиновой крошки, как и других посторонних включений, делает рассматриваемый материал многофазным, т.е. трудно говорить про его монолитность. При этом, даже приняв во внимание, что крошка сможет в процессе изготовления “присоединится” к связующему полиизоцианатному связующему композиции, из-за неравномерности распределения активных центров по поверхности, а также различного параметра растворимости, ухудшающего совмещение различных материалов, в т.ч. из-за использования в одной системе каучуков разных типов, трудно обеспечить, чтобы каждая частица резиновой крошки была полностью “покрыта” связующим. Поэтому в массиве готового “антивибрационного” материала всегда присутствуют микропоры. Справедливость этого утверждения подтверждают показатели плотности виброрезов — 730 кг/куб.м, что в 1,5 — 2 раза ниже, чем у классической монолитной резины. А так как резиновая крошка распределена во всем объеме связующего материала, в том числе и на поверхности, очевидно, что виброрезы представляют собой систему с большим числом открытых пор.
Чаще всего виброизолирующие материалы укладывают под фундаментами зданий или под оборудованием, т.е. либо в землю, либо в нишевые пространства, которые обычно слабо вентилируемые, и лежат, как правило, ниже уровня пола. В таких условиях невозможно избежать воздействия на виброзащитный материал воды. При этом будет иметь место не набухание самой резины в воде (к чему большинство резин достаточно устойчивы), а «механическое» проникновение воды в имеющиеся в материале микропоры.
В зависимости от размеров резиновой крошки, распределения частиц разного величины в массиве материала и количества воды, оказавшейся внутри массива композиционного материала, эксплуатационные характеристики изделия меняются. При этом вода — практически несжимаемый материал, и ее появление внутри материала в первую очередь серьезно изменяет динамические характеристики изделия. При отрицательных температурах вода, находящаяся в внутри микропор, за счет увеличения своего объема может вызывать трудно прогнозируемые разрушения структуры материала. Надо помнить также о низкой стойкости полиуретанового клея к гидролизу, влияние которого еще сильнее от присутствии в воде растворенных солей. А так как гидролитического действия воды и растворов солей на изоцианатный полимер будет трудно избежать в условиях эксплуатации, в частности в фундаментах, такой комплекс негативных воздействий приведет вначале к снижению эффективности виброзащиты, а затем и к разрушению системы виброизоляции.
Если очень нужно, то можно и приврать
Маркетологи, придумавшие товар под названием виброрез, объявляют его “аналогом” импортных виброизоляционных материалов, в частности полиуретановых Sylomer, Vibrafon и даже Nowelle, прекрасно осознавая, что это прямое введение в заблуждение потребителя. Любой специалист и даже квалифицированный потребитель объяснит, что материал из резиновой крошки и уретанового связующего имеет мало общего как с пенополиуретанами от Getzner и Kriburg, так и с нитрильными эластомерами типа Nowelle или ВЭП.
Очевидно, что заявляемые “антивибрационные материалы” проигрывают специально разработанным демпфирующим эластомерам как на основе нитрильных синтетических каучуков, так и пенополиуретанам, поскольку материалы из шинной крошки имеют низкие показатели как несущей способности, так и способности к поглощению вибрационных колебаний.
Традиционные же вулканизованные эластомеры, в т.ч. ПД-С-Ф, монолитны, практически не впитывают воду и устойчивы к гидролизу. Т.е. можно говорить о надёжности современных вибродемпфирующих эластомерных пластин изготовленных на основе бутадиен-нитрильных каучуков
Таким образом, наличие в “антивибрационном экоматериале” резиновой крошки, обычно приводит к нестабильности технических показателей продукта и приводит к ухудшению эксплуатационных, в т.ч. демпфирующих свойств материала. Применение в качестве базового материала высокоэластичного эластомера — крошки из резины на основе каучуков изопренового, дивинильного и бутадиен-стирольных, в принципе не позволяет получать виброзащитный материал с высокими показателями поглощения энергии колебаний, т.е. материалы класса виброрезов лучше не называть вибродемпфирующими.
Надолго ли изделия из крошки может хватить?
Посмотрим на прогнозируемые сроки эксплуатации виброрезов. Они не превышают, судя по их паспортным данным, 5 лет. Но производители предлагают применять их в фундаментах зданий, что видится очень смелым решением, если учесть срок эксплуатации некоторых сооружений рассчитывается не на один десяток лет. Что делать потребителю по истечение той самой “гарантийных” пятилетки — сложный вопрос.
Для сравнения — аналогичные показатели для классических демпфирующих эластомерных пластин, которые составляют по экспериментально-прогностическим исследованиям от 30 до 50 лет и более.
Вечная участь потребителя — выбор
И что делать в такой ситуации потребителю, которому нужно решить проблему с беспокоящими его шумом и вибрацией? Остаётся пойти на риск применения дешёвого, но нестабильного материала с мало предсказуемыми эксплуатационными характеристиками типа виброрез, изготовленного на 90% из отходов и материалов со свалки — сомнительное, но довольно экономичное решение. Другой путь — сделать разумный выбор в пользу качественного, надёжного классического вибродемпфирующего материала, к примеру демпфирующая эластомерная пластина ПД-С-Ф-10-500х500, разработанного специалистами НИИЭМИ и производство которой ведется в соответствии с ТУ 22.19.20-133-75233153-2022, который обеспечит вибрационную защиту объектов на десятки лет.