Производство эбонитовых изделий
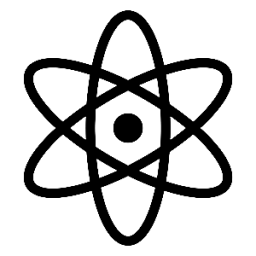
Эбонитовые пластины, стержни и трубки (ГОСТ 2748—53). Э б о н и т о в ы е пластины представляют собой листы длиной 1000—500 мм, шириной 500—250 мм и толщиной 0,5—32 мм. Эбонитовые пластины толщиной свыше 1,5 мм изготовляют дублированием необходимого количества листов эбонитовой смеси. Дублирование производят на гладкой, стальной или чугунной плите; листы прикатывают во всю их ширину тяжелым роликом. На изготовленную пластину с обеих сторон накладывают листовое олово толщиной 0,2—0,8 мм (в зависимости от толщины пластины). Для лучшего прилегания оловянных листов к поверхности пластин листы эти слегка смазывают керосином.
Тонко прокатанные зеркально гладкие листы олова предохраняют пластину от непосредственного действия вулканизационной среды, обеспечивают гладкую поверхность и хороший отвод тепла. На поверхности пластин из смесей на синтетическом каучуке иногда наблюдается небольшая шагреневость. Применение мягчителей — растительных и минеральных масел — в этих смесях снижает такой дефект. Перед дублированием каландрованные эбонитовые смеси выдерживают в роликах 8—12 ч. Выдержку (12—24 ч) применяют и для покрытых оловом пластин, укладываемых друг на друга.
Таким путем пластины подпрессовываются и получают усадку. Заготовки для эбонитовых пластин толщиной до 3—4 мм можно выполнять одновременно с листованием и дублированием смеси на каландре. Олово при этом прокатывают дублирующим валком со стороны нижнего валка каландра. Затем на другую сторону пластины вручную накладывают второй лист олова, пропускают пластину через дополнительный двухвалковый каландр и разрезают заготовку на отдельные пакеты.
Пачки эбонитовых пластин загружают в бак из дюралюминия, помещенный на тележке вулканизационного котла, подвешивают их на дюралюминиевых рейках или трубках, положенных на стенки бака, и наполняют водой, соблюдая, чтобы расстояние пластин от поверхности воды, дна и стенок бака составляло 100— 120 мм.
Вулканизация в воде обеспечивает равномерный нагрев пластин и лучший отвод выделяющегося тепла. Режимы вулканизации зависят не только от рецептуры смеси, но также и от размеров пластин и конструктивных особенностей котла. Толстые пластины вулканизуют длительно, применяя цикловую вулканизацию (прерывную, с промежуточным охлаждением). Однако разрыв процесса вулканизации в начальной стадии недопустим и ведет к отрыву олова и порче поверхности пластин. С пластин, выгруженных из котла, снимают олово. Если при этом возникает необходимость, пластины подвергают правке, прокладывая между ними хромированные стальные листы.
Для удаления с поверхности пластин блесток отслоившегося олова пластины дополнительно обрабатываются 10—15%-ной соляной кислотой. Остатки кислоты тщательно нейтрализуют и удаляют. Листы олова, снятые с пластин, используются повторно не более одного раза, а затем направляются в переплавку и прокатку. При плавке тщательно удаляют окись олова, так как она является главной причиной образования блесток. Олово отливают в плитки размером 20 X 30 см и толщиной 10—15 см. Плитки прокатывают на мощном двухвалковом каландре с гладкой поверхностью валков без фрикции.
Валки постепенно сближают до зазора 2 мм. Окончательную прокатку с приданием требуемого калибра- и блеска целесообразно производить на особом лощильном каландре с зеркально гладкими валками, применяя смазку их растительным маслом. Необходимость частой переплавки олова и связанная с этим потеря его, достигающая 1,5—2%, заставляет искать новые способы придания гладкости эбонитовой пластине. Рекомендуется применение алюминиевых листов толщиной 0,2—0,5 мм. Алюминиевые листы могут применяться повторно, но требуют после снятия их с пластин правки в прессе.
Возможно применять прессовую вулканизацию пластин. Дублированную с некоторым припуском по толщине пластину, не покрывая оловом, укладывают в нагретую и слегка смазанную льняным маслэм форму. Форма изготовляется из полированных листов алюминия или стали и окаймляется стальной рамкой соответственной высоты.
На Ленинградском заводе РТИ операции призводства эбонитовых пластин организованы в едином производственном комплексе. Заготовка пластин гроизводится на дублировочном станке, выполняющем операции: дублирования, обрезки кромок и прикатки оловянных листов. Подготовленные пластины комплектуются в специальные рамки и мостовым краном, пачкой, загружаются в ванну, которая лебедкой закатывается в вулканизационный котел.
После вулканизации эбонитовые пластины освобождаются от оловянной фольги и помещаются в кассету из фторопласта. Кассета тем же краном передается в облицованную фторопластом травильную панну с полуавтоматическим управлением процессами: заливки соляной кислотой, спуска кислоты, промывки пластин водой, сушки их теплым воздухом.
Олово для изготовления фольги плавится в том же помещении, в поворотной тигельной печи.
Эбонитовые стержни (палки) стандартных размеров изготовляют диаметром 5—75 мм и длиной до 300 см. Заготовку стержней производят профилированием на червячном прессе. Далее следует резка заготовок на отрезки требуемой длины и охлаждение в воде. Охлажденные заготовки помещают в трубки из дюралюминия толщиною стенок 1—2 мм и диаметром на 1,5—2 мм больше, чем выпускаемый стержень. Перед вулканизацией заготовки выдерживают в трубках 8—12 ч для завершения усадки, вулканизация эбонитовых стержней производится в котлах, в ваннах, наполненных водой. Между стенками ванны и дорнами помещают уплотняющий материал.
Еще недавно заготовки вулканизовали, забинтовывая их в мокрую ткань и подвешивая в баке, на таком расстоянии одну от другой, чтобы была обеспечена достаточная водяная прослойка. Стержни, вулканизованные в подвешенном состоянии, несколько деформировались при выгрузке и требовали последующей правки. Поверхностный слой стержней, вулканизуемых в условиях возможного доступа воды, значительно изменяется вследствие набухания. Отдача тепла таким слоем увеличивается, поэтому он остается менее вулканизованным, более мягким и рыхлым, чем внутренний слой, и более светлым.
Последнее объясняется тем, что на бухшие при вулканизации частицы дальше отстоят одна от другой. Интенсивность цвета ослабляется. Оборачиваемость тканевой обертки была лишь двукратная, тогда как алюминиевые трубки служат до полугода. Поскольку стержни применяются в качестве поделочного материала, поверхностный слой их заводом-изготовителем обычно не снимается. В случае специальных требований потребителей обточка и калибровка стержней производятся обработкой их в специальных бесцентровых шлифовальных станках.
Эбонитовые трубки стандартных размеров изготовляют внутренним диаметром 3—50 мм, толщиной стенки 1,1 —12,5 мм и длиной не менее 400 мм. Трубки этих размеров заготовляют профилированием на червячном прессе; трубки большего размера, с значительной толщиной стенки, изготовляют викелеванием. Заготовки надевают на дорны и закатывают в ткань.
Аккумуляторные баки и детали. Эбонит как диэлектрик нашел особо широкое применение в производстве аккумуляторов. В кислотных аккумуляторах эбонитовыми деталями являются: бак, сепараторы (прокладки между смежными пластинами) и формовые детали — крышка с пробками и втулками. В трубчатых аккумуляторах, применяемых для электровозов, положительные электроды в своей основе имеют металлическую рамку (из сплава свинца с сурьмой) с промежуточными вертикальными стержнями, на которых надета перфорированная эбонитовая трубчатая пластина-панцирь (рис. 99). В пространстве между стержнем и перфорированной стенкой помещают активную массу.
Баки. Различают два типа эбонитовых аккумуляторных баков: од-ногнездные и многогнездные. Одногнездные баки изготовляют как ручной клейкой, так и формованием. Многогнездные баки (моноблоки), содержащие 3, 6, 12 и более гнезд, изготовляются формованием (ГОСТ 6980—54). Баки больших и некоторых средних размеров клеят на алюминиевых моделях, соответствующих по форме и размерам полости баков, с припуском на усадку. В целях повышения прочности и электроизоляционных свойств стенки баков иногда армируют, например стеклотканью. Клееные баки вы ходят из употребления, уступая место моноблокам, как более портативным в условиях применения, так и более прогрессивным по технологии их производства.
Развитие производства многогнезд-ных аккумуляторных баков вызвано ростом автомобильной и авиационной промышленности. В целях снижения себестоимости формовых аккумуляторных автомобильных баков, ускорения их вулканизации и повышения теплостойкости применяют эбонитовые смеси, содержащие регенерат, минеральные наполнители, а также некоторые виды пластмасс и эбонитовую пыль. Вулканизация таких эбонитовых Смесей может проводиться при температуре до 170 С за 20—25 мин, в зависимости от введенного в смесь ускорителя и размеров изделия.
Формование и вулканизация баков производятся на специальных гидравлических прессах в особых пресс-формах. Форма состоит из матрицы, определяющей наружные габариты бака, укрепляемой па нижней плите пресса, и пуансона, оформляющего полость бака и межгнездные перегородки и прикрепляемого к верхней плите.
Матрица имеет днище и четыре откидные стенки (щеки). Для удержания в вертикальном положении стенок матрицы в период формования и вулканизации бака между плитами пресса помещена подвижная траверса, имеющая пирамидальную полость. На отечественных заводах применяются прессы П-457 Серпуховского завода с верхним расположением гидравлического цилиндра (рис. 100). Известны также прессы с обычным, нижним, расположением этого цилиндра и верхней, неразъемной матрицей.
Для изготовления баков малых или средних размеров применяют формы, рассчитанные на выпуск нескольких баков, или помещают в пресс несколько единичных форм.
Испытание аккумуляторных баков. Аккумулятор-пые баки должны быть герметичны. Отсутствие в них мельчайших сквозных отверстий определяется испытанием электрическим током. Для такого испытания берут водопроводную воду. Испытание баков среднего размера проводится при напряжении 10—15 кВт, длительность испытания 10—15 с. Баки больших размеров ответственного назначения испытывают при напряжении 48—50 кВ в течение 16 с. В этих условиях металлические и иные включения выгорают, и в местах образующихся пустот происходит пробой бака.
При эксплуатации аккумуляторных батарей вследствие тепло-пых процессов нагревается электролит, а отсюда и баки. Это может вызвать выпучивание стенок бака, смещение пластин и порчу аккумулятора. Поэтому баки, имеющие особое назначение, испытывают на теплостойкость путем измерения величины выпучивания стенок: первоначально при наполнении бака холодной водой, а затем после подогрева воды до температуры, предусмотренной техническими условиями.
Сепараторы перфорированные. Для устранения контакта между разноименными пластинами, не нарушая доступа электролита к пластинам, в электрических аккумуляторах применяют сепараторы. Эбонитовый сепаратор представляет собою тонкий перфорированный эбонитовый лист, снабженный упрочняющими продольными ребрами. При сборке аккумулятора он накладывается на положительно заряженную пластину. В блоке с ним помещают сепаратор с микропорами, примыкающий к отрицательно заряженной пластине. Такие сепараторы изготовляют из тонких листов ольховой фанеры.
В иных случаях применяют ребристый эбонитовый сепаратор и гладкую фанеру. Производство эбонитовых сепараторов близко к изготовлению эбонитовой пластины тонких калибров. Для изготовления сепараторов без ребер на каландрованные листы эбонитовой смеси сверху и снизу накладывают листы олова и полученные пакеты вулканизуют в котле острым паром. После снятия олова и усадки эбонитовые листы обрезают, согласно требуемым размерам, а затем следует пробивка отверстий на перфорационной машине. Перфорационная машина представляет собою штамп-пресс эксцентрикового типа с прерывной автоматической подачей материала посредством рифленых валиков.
Штампующую часть пуансона составляют два ряда сталь-I ных закаленных штифтов, расположенных в шахматном порядке. Матрица имеет два ряда отверстий, соответствующих штифтам пуансона. Шаг подачи регулируют так, чтобы расстояние между центрами отверстий по длине листа было одинаково с расстоянием между штифтами пуансона.
Ребристые эбонитовые сепараторы заготовляют профилированием каландрованных листов, дополнительно пропуская их через профильный двухвалковый каландр. Нижний валок каландра гладкий, а верхний имеет узкие канавки. Перед пропуском через профильный каландр лист эбонитовой смеси накладывают на оловянный лист, обеспечивая гладкость сепаратора; толщина листа ребристого сепаратора 0,5—Э,6 мм, а высота ребра 2—3 мм. Наличие ребер сокращает перфорированную площадь сепаратора, поэтому ребристые сепараторы иногда заменяют гофрированными. Хрупкость, свойственная эбонитовым сепараторам, составляет существенный их недостаток.
Сепараторы микропористые. Действие аккумуляторной кислоты (серная кислота, плотность 1,28 г/см3) и повышенная температура вызывают довольно быстрый износ фанерных сепараторов. Вместо них в последнее время применяют сепараторы из микропористого эбонига, более стойкого в условиях работы аккумуляторов.
В последнее время на смену микропористым и перфорированным сепараторам приходят микропористые сепараторы из пластических масс, более гибких и менее хрупких, например пластмассовые сепараторы из полихлорвинила.
Формовые эбонитовые изделия. К числу многообразных эбонитовых изделий относятся: фасонные крышки аккумуляторных баков, втулки, пробки и гильзы трубчатых пластин, а также детали для магнето, изделия для предприятий химической промышленности, производства искусственного шелка и т. п. Заготовки для формовых эбонитовых изделяй выполняются описанными ранее приемами. Значительная усадка, свойственная эбонитовым смесям, требует соответственного увеличения полости формы. В тех случаях, когда вулканизованные изделия подвергаются последующей механической обработке, необходимо обеспечить достаточные припуски.
Так как процесс вулканизации мало наполненных эбонитовых смесей отличается больней длительностью, то для ускорения оборота форм вулканизацию иногда проводят в два приема. Кратковременной подвулканрзацией в прессе оформляют изделие, придавая ему прочность, достаточную для выемки из формы без повреждений. Последующей свободной вулканизацией в котле придают изделию необходимую твердость. Применение наполненных смесей с ускорителями при вулканизации в прессах, обогреваемых ч, о 160—170 °С, позволяет ограничиться вулканизацией в один прием.
При конструировании форм для изделий, вулканизуемых в два приема, необходимо предусматривать припуск на усадку, несколько больший, чем у изделий одноразовой вулканизации, так как оба процесса сопровохдаются усадкой.
Введение талька и других наполнителей не ухудшает «распрессовки», а способствует лучшей текучести эбонитовых смесей при запрессовке форм.
Правка формовых эбонитовых изделий. Как и в производстве эбонитовых пластин, в ряде случаев применяется правка формовых аккумуляторных баков и эбонитовых изделий. Для этого изделия, нагретые в шкафах или на плитах, обогреваемых паром, закладывают в соответственную правку, зажимают в ней и охлаждают затем до 20—25 °С. Особо большое значение имеет правка в производстве формовых эбонитовых изделий с резь бой.
Раньше такие изделия изготовляли, применяя станковую обработку (обточку, нарезку, шлифовку и т. п.). С введением правки вулканизованные в соответственных формах изделия по обрезке заусенцев вновь нагревают, ввертывают в правки с нарезкой и охлаждают в них.
Клееные эбонитовые изделия. Эбонитовые трубы, тройники, угольники, краны и другие изделия изготовляют преимущественно ручной клейкой с последующей механической обработкой.
Эбонитовые трубки с фланцами или без них, например полые цилиндры диаметром 800 мм и длиной 1500 мм с толщиной стенки 30 мм для пусковых реостатов к блюмингам, изготовляют посредством накатки на дорнах. Перед вулканизацией трубы плотно закатывают бинтами, применяя спиральную накладку ткани. Иногда трубы вулканизуют без дорна, наполнив их мелким речным песком и закрыв концы деревянными пробками. В этих пробках сделаны небольшие отверстия, чтобы дать возможность воздуху оставшемуся в трубе, постепенно, по мере его нагревания и расширения, выйти из трубы.
Если требуются изогнутые трубы, то по соответственным лекалам выгибают наполненные песком и разогретые трубы. В случае необходимости изготовления труб, изогнутых без складок или с малым радиусом кривизны, применяют соответствующие цинковые дорны с последующим растворением цинка путем обработки готового изделия в соляной кислоте.
Однако неформовые, вулканизуемые в котле эбонитовые изделия могут иметь лишь относительно несложную конфигурацию, так как размягчение эбонита в начальной стадии вулканизации может повлечь изменение вида и размеров изделия. Отсюда наполнение эбонита целесообразно не только для удешевления, но и в целях устойчивости габаритов сырых заготовок, а также для устранения пор и уменьшения усадки.
Эбонитовая пыль. Эбонитовые лом и отходы поступают в цех размола эбонитовой пыли, где подвергаются сортировке для разделения материалов, дающих эбонитовую пыль 1 и 2-го сортов, а.также для устранения посторонних предметов и материалов, не идущих в размол. Крупные предметы и большие куски лома дробят на меньшие куски вначале на щековой, а затем на молотковой дробилках. Далее на магнитном сепараторе отделяют металлические включения. Дробленый материал поступает на рифленые вальцы, где он размельчается в крупу, а затем передается на гладкие вальцы с большой фрикцией, где размалывается в пыль. Поскольку металлические включения не вполне удаляются при первом пропуске через магнитный сепаратор или попадают в пыль вовремя размола вследствие срабатывания поверхности валков, необходимо полностью их удалить.
Удаление металлических включении нз эбонитовой пыли производят на втором магнитном сепараторе; иногда на первый пропуск направляют крупу, полученную размолом на рифленых вальцах. Далее следует просев на вибрационных ситах, устанавливаемых под гладкими вальцами. В процессе размола на вальцах эбонитовая пыль сильно нагревается. Разогретая пыль способна к самовозгоранию; смесь ее с воздухом может дать взрыв.
Нижним пределом взрыва эбонитовой пыли 1-го сорта М. Г. Годжелло называет 7,6 сН/м3, а серы (серного цнета)—2,3 сН/м3. Так как к 1-му классу (с наибольшей взрыво-опасностыо) относятся аэрозоли (взвеси) с нижним пределом до 15 сН/м3, то размол и просев названных продуктов и улавливание эбонитовой пыли требуют особой осторожности. Концентрация эбонитовой пыли в момент взрыва, при наличии раскаленного тела, составляет 40 сН/м3. Поэтому размолотую пыль необходимо охладить. Для охлаждения пыль распределяют на гладком полу или на специальном охлаждаемом снизу железном помосте слоем 5—6 см.
Вместо просева на ситах можно применять отвеивание пыли, которое необходимо производить в герметизированной аппаратуре в среде нейтрального газа.
Хранение эбонитовой пыли требует особой осторожности. Покушение пыли и образование комков сигнализируют о начинающемся горении. Влажность пыли, большая 0,5%, благоприятствует самовозгоранию. Отсюда в помещениях, где перерабатывается и хранится эбонитовая пыль, следует допускать относительную влажность воздуха 45—50%. Технические условия на эбонитовую пыль 1-го сорта не допускают зольности свыше 10%, а для пыли 2-го сорта — свыше 30%.
Иногда потребность в эбонитовой пыли 1-го сорта не обеспечивается наличием соответственных эбонитовых отходов и лома. В таких случаях практикуют изготовление специальных эбонитовых пластин и последующий размол их. Эбонитовую пыль изготовляют из ненаполненных вулканизатов мягкой резины путем размола их, добавления серы и последующей вулканизации до образования эбонита. Этот же путь позволяет получить низшие сорта эбонита из регенерата или из старой резины.
Асбесто-резиновые изделия. Известен ряд твердых изделий, получаемых на базе каучуковых смесей, но отличающихся от эбонита значительным содержанием волокнистого минерала наполнителя-асбеста.
Пластины с волокнистым наполнителем. Паронит — листовой материал, применяемый для изготовления прокладок для уплотнений в среде перегретого и насыщенного пара, горячего воздуха и газов, щелочных растворов, слабых кислот, аммиака, масел и погонов нефти. Паронит (ГОСТ 481—58) состоит из 60—70% асбестового волокна, 12—15% каучука, 15—18% минеральных наполнителей и 1,5—2,0% серы.
Для прокладок применяют также паронит марки Л, изготовляемый из асбеста, латексного каучука и наполнителей. Для приготовления паронита (резинопаронита) в клеемешалке готовят клей из каучука и бензина, а затем добавляют каолин, красящие вещества, серу и, наконец, асбест. Полученная густая паста обрабатывается на так называемых иттовых вальцах, у которых диаметр заднего валка значительно больше, чем диаметр переднего.
Задний валок обогревается паром, передний охлаждается. Резиновая паста постепенно покрывает задний валок и, по мере испарения бензина, уплотняется на нем. Вальцованную пластину срезают в форме листа с заднего валка. Толстые листы паронита получают из тонких путем склейки и дополнительной прессовки в гидравлическом прессе.
Электронит — листовой материал, изготовляемый из асбестового волокна и синтетического каучука, применяется для теплостойких электроизоляционных прокладок.
Тормозные асбестовые накладки применяются для обеспечения необходимой силы трения при торможении автомобилей, автобусов и тракторов, а также для удержания машин на месте во время стоянок. Такие накладки изготовляют из смесей, содержащих асбест, каучук и пластические массы.
Асбоцементные плитки для полов промышленных сооружений относятся к числу многих изделий, изготовляемых на основе отходов старой резины. Им свойственны значительная химическая стойкость и высокая износостойкость, превышающая истираемость метлахских плиток.