Обработка тканей и резиновых смесей на каландрах
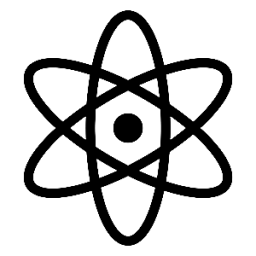
Сушка и промазка тканей. Ткани, применяемые в производстве ремней, рукавов и других изделий, промазывают резиновой смесью.
Если для промазки на каландр поступает относительно толстая ткань, например, бельтинг или чефер, то необходимо ткань предварительно нагреть и просушить. Нагрев ткани облегчает процесс промазки, так как размягченная резиновая смесь легче проникает В теплую ткань. Удалением влаги улучшают адгезию резиновой смеси к ткани и предупреждают расслаивание изделия, возможное в результате выделений водяных парой в процессе вулканйзйцйй. Сушат ткани на сушильных барабанах, монтируемых из 6 или 8 барабанов в комплекте. Над барабанами, на расстоянии 2 м от пола, следует устанавливать зонты вытяжной вентиляции. Для заправки ткани на барабаны применяют заправочные тканевые полосы или ленты, оставляемые в машине по окончании работы. Сушильные барабаны обогреваются паром. Обычно ткани сушат при температура на поверхности барабана около 115°С и скорости движения ткани 25—28 м/мин. В этих условиях, в зависимости от количества пропусков через барабаны, влажность ткани снижается с й 7 до 2,5-2,0%.
Для осуществления непрерывного процесса сушки два, а иногда и три комплекса сушильных барабанов целесообразно соединять в один агрегат. Для обеспечения соединения кусков ткани в общий рулон, не останавливая работы агрегата, второй конец каждого куска ткани на длине 5—б м Должен быть предварительно на ткацкой фабрике сложен вдвое. Таким образом, конец ткани освобождается несколько раньше раскатки всего рулона ее и создается возможность соединения этого конца с передним концом следующего рулона ткани. Концы их сшивают однониточньш швом встык на специальной швейной машине, позволяющим легко разделить сшитые куски при выходе ткани с агрегата, или склеивают резиновым клеем с последующей вулканизацией шва. Накатку просушенной ткани необходимо вести с той же скоростью, с какой ткань проходит по барабанам. Контроль влажности ткани производят или периодически, досушивая образцы определенное время до постоянной массы или непрерывно — посредством специальных электровлагомеров. Сушка, однако, понижает прочность ткани.
При промазке ткани разогретую резиновую смесь наносят на поверхность ткдни и втирают в нее на трехвальных промазочных каландрах. Отношение окружных скоростей валков каландра колеблется в пределах от 1: 1,3 до 1: 1,7, но обычно равно 1: 1,5. Ткань промазывают с обеих сторон; лишь в отдельных случаях, например при изготовлении одного из видов изоляционной ленты, применяют одностороннюю промазку. Если вторая сторона ткани промазывается на том же каландре, где обрабатывалась первая ее сторона, применяют промазку по схемам, приведенным на рис. 1. Для этого необходимо кроме роликов 1 и 2 иметь добавочный приемный ролик 3, направляющий ролик 4 и тормозное приспособление у приемного ролика 2. На каландрах с валками большой длины можно одновременно обрабатывать две полосы ткани. Заправку их производят по приведенной схеме, но не синхронно по фазам обработки, а смещая их.
Иногда сушильные барабаны устанавливают в агрегате с каландром, помещая между ними компенсатор. В этом случае просушенная ткань незамедлительно поступает на промазку. Если же между сушкой и промазкой ткани имеется разрыв во времени 30—60 мин, ткань следует сохранять в особых камерах с температурой 50—60 °С. Иногда у промазочных каландров для дополнительной подсушки ткани, поступающей в каландр, устанавливают обогреваемые паром барабаны.
Особенности обработки текстиля из вискозы и синтетических волокон. Применение вискозных и синтетических текстильных изделий (ткани, корда, пряжи) (см. главу 9) в производстве РТИ требует предварительной их обработки для создания системы текстиль — адгезив — резина, так как адгезия к резине гладких цилиндрических волокон недостаточна. Образование такой адгезивной пленки производится при помощи пропитки текстиля в соответствующих составах и последующей механической и тепловой обработок.
Пропитка вискозных материалов производится латексно-резор-цин-формальдегидным комплексом. Применяется бутадиен-стирольный или наиритовый латекс. Резорцин-формальдегидная смола приготовляется непосредственно перед применением путем конденсации резорцина и формальдегида в водной среде в присутствии едкой щелочи. Пропитка и последующая сушка при повышенной (130°С) температуре производится на агрегатах типа ИРУ-18, АЛТ-22 и др.
Пропитка полиамидных материалов — изделий из капрона и анида — проводится в подобных же составах, но с применением активных латексов: бутадиен-метилпиридинового или же карбокси-латного, а также наиритового. Ввиду свойственной полиамидным материалам усадки при тепловых обработках, пропиточные агрегаты усложняются наличием камер горячей вытяжки и камер фиксации материала.
Применяются, но менее эффективны, пропитки полиамидного текстиля в водных растворах смолы Э-89, получаемой путем конденсации эпихлоргидрина и ж-фенилендиамина в эквимолекулярных соотношениях в водной среде. Более целесообразно применять такую пропитку для резин нз полярных каучуков, например наирита.
Являются перспективными и разрабатываются способы повышения прочности связи, непосредственно между текстилем и резиной, путем введения в состав резиновых смесей низкомолекулярных соединений некоторых фенолов с уротропином (например, «резотропин»).
Пропитка полиэфирных материалов — текстильных изделий, изготовленных из лавсана, —представляется более трудной. Вследствие высокой гидрофобности этих волокон латексно-резорцинфор-мальдегидная дропитка мало успешна, а поэтому применяется пропитка органическими 20% растворами полиизоцианатов, например лейконата (см. главу 5).
Ввиду значительной, до 15%, усадки полиэфирного волокна при 150°С, необходима термофиксация таких изделий. Поскольку полиэфирные волокна и изделия из них имеют высокий модуль, наиболее целесообразно термофиксацию проводить сразу после изготовления пряжи, до операции ткачества.
Пожаро- и взрывоопасность, а также и токсичность пропиток на органических растворителях ведет к поискам приемов пропитки модифицированными изоцианатами. Такие «блокированные» изоцианаты дают водные эмульсии, пригодные для пропитки. После сушки при 130—140 °С следует нагрев до 180—200 °С, при котором блокированные изоцианаты разлагаются, выделяя активную форму.
Применяется двусторонняя клеепромазка полиэфирного текстиля, вначале клеем, содержащим изоцианат в составе резино вой смеси, а затем резиновым клеем без изоцианата; одним из недостатков этого способа является структурирование каучука изоцианатом, приводящее к быстрой желатинизации клея. При пропитке полиэфирных материалов применяется так называемая двухстадийная пропитка: вначале в 3—5% растворе изоцианата в органическом растворителе, затем сушка и вторая пропитка в латексно-резорщшформальдегидном составе.
Расправители и вводчики ткани. Для расправления продольных складок на ткани и уменьшения усадки ткани по ширине и вытяжки пс длине перед сушильным барабаном и каландром устанавливают ширительные приспособления. Имеются ширители (вводчики), ксторые одновременно направляют, центрируют ткань. В автоматическом вводчике ткани системы Фоксвел кромки ткани зажимаются между двумя парами наклонно расположенных роликов. Пневматический прижим обеспечивает контакт нижнего ролика с верхним. При отклонении ткани в ту или другую сторону соответственшя кромка ткани задевает рычаг, связанный с клапаном пневматического устройства, воздух выходит и нижний ролик освобождает ткань. Тогда ткань, оставшаяся под действием второй пары роликов, перемещается к центру. Для работы этого вводчика обязательно наличие достаточно жестких кромок ткани.
Применяется также устройство, состоящее из ролика, подшипники которого смонтированы на раме, имеющей ось вращения. Ось вращения рамы выбрана такой, что при качании рамы, а следовательно и ролика, ткань, проходящая через ролик в зазор калипдра, приподнимается по краям. Оси ролика и валков каландра и что время скрещиваются; вследствие этого одна сторона ткани растягивается больше другой, и ткань стремится переместиться в этом направлении. За перемещением ткани следит щуп, постоянно касающийся кромки ткани. Щуп связан с регулирующим устройством типа сопло-заслонка. Это устройство передает импульс на регулирование к исполняющему органу — пневмоклапану, снизанному своим штоком с роликом качающейся рамы; ролик поворачивается в другую сторону, ткань начинает перемещаться и противоположном направлении. Таким образом рамка с роликом, непрерывно качаясь, не дает ткани отойти от центральной оси. Применяется также и фотоэлектрический контроль правильного положения кромки раскатываемой ткани.
Изменение размеров ткани при промазке. В процессе промазки ткань вытягивается и сдавливается, значительно изменяясь по длине и толщине. Как видно из табл. 1, ткань, растянутая во время промазки, в последующем дает усадку 1—4%, но все же сохраняет значительную часть полученного удлинения. Увеличение длины промазанной ткани объясняется тем, что вытяжка идет, в основном, за счет остаточного удлинения ткани; заполнение же ткани резиновой смесью механически препятствует возврату упругих растяжений. Величина вытяжки ткани и последующей усадки зависят от вида ткани, сорта резины и режима работы каландра. Данные табл. 1 относятся к смеси с содержанием до 50% каучука. Смеси с ббльшим содержанием каучука труднее проникают в толщу ткани, дают меньший расход на промазку 1 м2 ткани; одновременно обнаруживается большая усадка ткани после промазки.
Увеличение длины промазанной ткани имеет существенное значение в планировании расхода текстильных материалов. Поскольку нормы расхода составляются по данным закроя в основных цехах, потребность тканей суровья (непрорезиненшйх) должна исчисляться с учетом изменения их площади при операциях обработки тканей на каландрах. Одновременно с увеличением длины ткань становится уже и плотнее по основе, нити основы выпрямляются, их натяжение становится равномернее, прочность ткани возрастает. Это увеличение может перекрыть то снижение прочности, которое получила ткань вследствие предшествующей просушки (см. главу 9). Однако относительное удлинение ткани при этом снижается, ее продольная жесткость возрастает.
Расход резиновой смеси на промазку тканей. Тканевые элементы конструкции резинотканевых изделий более жестки, чем резиновые, а поэтому воспринимают основную долю нагрузки, которая возникает в изделии в условиях эксплуатации. Однако если бы элементы, например слои бельтинга в ремнях, не были соединены в одно целое резиновой массой, они работали бы не одновременно, а следовательно, не эффективно. К тому же, если тканевые слои не были изолированы друг от друга резиновыми прослойками, они весьма быстро износились бы вследствие трения, возникающего при многократном изгибе, которому подвергаются изделия.
Должная изоляция может быть достигнута лишь при наличии достаточного резинового слоя между тканевыми слоями и при условие проникновения резины в ткань между нитями основы и утка и в толщу самих нитей. Количество резиновой смеси, которое можно нанести при промазке на ткань, зависит от вида смеси и от характера ткани. Более пластичная смесь легче проникает в толщу ткани; более рыхлая, менее гладкая ткань принимает большее количество резиновой смеси, обладает большей резиноемкостью (см. главу 9).
Все поры ткани заполнить резиновой смесью не удается, поэтому фактический расход резиновой смеси при промазке тканей ниже теоретической ее резиноемкости. Практически при промазке ткань в среднем принимает лишь 32—43% теоретически возможного количества резиновой смеси (считая на первоначальные габариты ткани). Если же поглощение резиновой смеси тканью оценивать с учетом уменьшения толщины ткани после промазки, то заполнение ткани составит 45—50%. Из общего количества резиновой смеси, расходуемой на промазку ткани, около 60—65% затрачивается при обработке первой стороны ткани и 40—35% — второй.
Накладка резиновой смеси на ткань. Накладка утолщенного слоя резиновой смеси необходима для усиления сцепления прорезиненных тканевых слоев (прослойки в некоторых видах плоских приводных ремней и в транспортерных лентах) для защиты тканевого слоя или для создания наружного покровного слоя. Дополнительные, толщиной около 0,3 мм, резиновые прослойки (сквиджи) между тканевыми слоями увеличивают прочность сцепления последних и обеспечивают большую гибкость изделия. Толщина, ббльшая 0,3 мм, не рекомендуется, так как при этом увеличивается поэможность расслоения из-за напряжения сдвига.
Дополнительную резиновую прослойку на ткань калибром 0,2—0,3 мм можно наложить, применяя третий пропуск через каландр с фрикцией или через листовальный каландр. Известен также способ наложения так называемой «фрикционной накладки». Достоинство этого способа состоит в возможности выполнения работы всего лишь за два прохода ткани через каландр. За первый проход промазывается одна сторона ткани, за второй — другая, с одновременной накладкой дополнительной прослойки. При этом отпадает операция отбора кромки резиновой смеси, неизбежная при работе на листовальном каландре. Однако этот способ требует применения мало распространенных каландров с небольшой фрикцией (около 1 :1,2—1 :1,3).
Накладка резиновой смеси на ткань для создания защитного или покровного слоев (например, при изготовлении различных видов кожзаменителей) производится так же, как и накладка прослоек. Пропуск же ткани через каландр связан со значительной ее вытяжкой и сдавливанием, а также с искажением рисунка ткани, что не всегда допустимо.
Обкладка ткани резиновой смесью. Резиновый лист, выходящий из каландра, можно наложить на ткань, не заправляя ее межд> валками каландра, а прижимая к каландруемому листу с помощью металлического дублировочного валка, обложенного эбонитом. Этот способ обкладки ткани позволяет более точно установить калибр резинового слоя, не изменяя размеров и вида ткани, поскольку ткань здесь идет без значительного натяжения (рис. 2). Наименьший вес накладываемой этим способом резины состав
ляет около 120 сН/м2, а потому в тех случаях, когда требуются более легкие покрытия, применяют клеепромазочные машины.
Рис. 2. Схема дублирования и обкладки на каландре.
Листование резиновой смеси. Широко применяемое в производстве РТИ листование (каландрование) резиновой смеси приводит к ориентации каучуковых и минеральных частиц в направлении каландрования.
Если такое расположение частиц остается закрепленным в материале, то наблюдается так называемый каландровый эффект; сопротивление такой резины разрыву по каландрования выше, чем в поперечном направлении, относительное же удлинение ниже. Когда резиновая пластина сходит с валки каландра, то деформирующее влияние адгезионных сил прекращается и силы упругой деформации вызывают сокращение (усадку) пластины в направлении каландрования и увеличение ее калибра. Это увеличение калибра особенно значительно для ненаполненных смесей на основе хлоро-пренового и бутадиен-стирольного каучуков и достигает 60—90% величины зазора каландра; наполнение смеси снижает усадку.
Так как съем каландрованного листа производится отборочным транспортером и закаточным устройством с той же линейной скоростью, что и листование, то усадка при этом не проявляется в полной мере и сказывается в последующих операциях, связанных с нагревом свободно лежащей пластины. Неоднородность материала, вызываемая каландровым эффектом, нежелательна. Повышение температуры нижнего (последнего) валка каландра снижает каландровый эффект; если же резиновая смесь оставляет каландр, соприкасаясь с охлажденным валком, каландровый эффект остается. Тугая закатка в прокладочную ткань сохраняет растяжение, полученное резиной на валках каландра, поэтому и каландровый эффект остается; закатка же в нагретую прокладку снижает каландровый эффект. К этому же приводит пропуск резинового листа в свободном (ненатянутом) состоянии на транспортере через теплую (60—65 °С) ванну. В производственной практике приходится выпускать за смену пластины различной толщины (от 0,5 до 4 мм) при ассортименте 8—10 смесей. Передовики производства разработали последовательность выполнения наряда, обеспечивающую высокий коэффициент машинного времени при точном пыполнении технологических регламентов. Работа начинается с выполнения более тонких калибров, что позволяет подогревалыцику-срезчику иметь резерв времени на разогрев очередной смеси, выпускаемой в более толстых листах. Переход от тонких к более толстым листам, учитывая при этом очередность резин по возрастанию температур обработки, облегчает труд и сокращает время на перестройки режимов.
Выпуск пластин значительных калибров за один проход не исключает отсутствия в них пузырьков воздуха; поэтому необходимо производить дублирование пластины из отдельных листов резиновой смеси не толще 1,5—1,0 мм.
Удобно производить дублирование на особом двухвалковом дублере, располагаемом за каландром (рис. 3). Посредством двух транспортерных лент, которыми оснащен дублер, резиновая пластина образует петлю и направляется в зазор дублирующих валков, где на нее наращивается выпускаемый каландровый лист.
Если требуется каландровать резиновый лист, подлежащий дальнейшем вулканизации в котле, применяется опудривание тальком во время движения листа по отборочному транспортеру с последующим удалением излишка талька. Для этой цели может быть применено электромагнитное вибрационное сито. Электромагнитное сито не имеет приводного механизма и трущихся частей, а потому удобно в обслуживании.
Подготовка прокладочных холстов составляет весьма важный участок каландрового цеха. Возвращаемую из цехов-потребителей подкладочную ткань следует обязательно очищать, пропуская ее через круглощеточную машину с одновременной накаткой на ролики; при чистке и накатке необходимо применять ширительные и расправляющие устройства. В целях предупреждения прилипания резиновой смеси к прокладочной ткани, последняя пропитывается различными химическими составами (асфальтовыми лаками, нитролаками и т. п.). Такая пропитка придает тканям большую гладкость. Однако пропитанная ткань становится более жесткой, появляющиеся на ней складки трудно разглаживаются и оставляют След па резине. Применение мыльных растворов или суспензионного опудривания каландрованных листов тальком или каолином может устранить необходимость прокладочных тканей.
Агрегирование каландров с оборудованием сборки заготовок. До последнего времени территориальное разграничение каландровых и сборочных цехов, связанное с необходимостью межцехового транспорта и значительным прокладочным хозяйством, было обычным на заводах РТИ. Теперь’ же каландры и обслуживающие их вальцы в ряде случаев устанавливаются в непосредственной близости с оборудованием, использующим каландрованные листы или промазанную ткань. Облегчая и упрощая транспорт и способствуя улучшению качества, подобное агрегирование ставит, естественно, съем с каландра в зависимость от производительности сборочного оборудования. Такое агрегирование осуществлено на ряде заводов в производствах: резиновой подошвы, напорных рукавов, приводных ремней и транспортерных лент, мячей и игрушек.
Контрольные и вспомогательные устройства у каландров. Для электрометрического определения влагосодержания могут быть использованы замеры объемного сопротивления ткани, величины, зависящей от влажности ткани. Возможна конструкция электровлагомера, основанная на измерении емкости и сопротивления. Такой прибор разработан и успешно применяется на заводе «Каучук». Датчик представляет плоскопараллельный конденсатор, состоящий из двух пластинок: неподвижной размером 110X70 мм и подвижной диаметром 10 мм, между которыми и помещают срезанный с рулона образец ткани. Влажность бельтинга таким прибором определяется с точностью ±0,1%.
Рулоны прорезиненной ткани следует контролировать как по длине, так и по массе. Для промера ткани промазочные каландры снабжаются измерительными каретками. Массу прорезиненной ткани или каландрованного листа рекомендуется проверять непрерывно на автоматических весах. Весы состоят из двух деревянных или металлических роликов, расположенных на расстоянии около 2 м, определяющих длину взвешиваемого куска. Посредине между этими роликами расположен металлический валик меньшего размера, связанный с коромыслом весов. Весы снабжены электрическими контактами и стрелкой, сигнализирующими об отклонениях в массе каландруемого материала.
Автоматический контроль толщины листа. Толщину каландруемого листа можно контролировать автоматически. Электромагнитные или индуктивные калибромеры основаны на принципе изменения магнитного поля прибора в результате отклонения в толщине каландруемого листа, проходящего через прибор; точность замеров ±0,03 мм. Применяются также калибромеры механического действия, непосредственно замеряющие величину отклонения калибра листа или с электрической передачей замера на расстояние.
В настоящее время для бесконтактного непрерывного контроля толщины резиновых листов находят применение радиоактивные изотопы, в частности криптон 85. Измерение основано на том, что с изменением толщины каландруемого листа изменяется интенсив* и ость проникающей через него радиации.
Автоматические калибромеры могут быть снабжены записывающим прибором. При оснащении каландров приборами автоматического ^гулирования зазора валков сущность устройства сводится к следующему: малые токи, протекающие в электрической цепи калибромера, с помощью электронных преобразователей и усилителей превращаются в токи большой величины, способные воздействовать на магнитные устройства, управляющие работой моторов, производящих перемещение подвижных подшипников валков каландра. Автоматический калибромер-регулятор, применяющий пневматический датчик, создан в Научно-исследовательском институте резиновой промышленности.
Температурные условия переработки резиновых смесей на вакуум-машинах рассмотрены в работе.