Вулканизационные формы
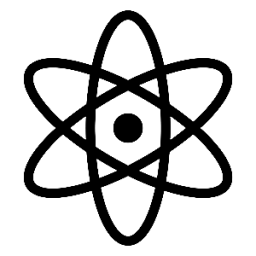
Конструкции вулканизационных форм. Вулканизационные формы должны отвечать определенным производственным требованиям. При выборе материала для них необходимо учитывать: устойчивость к сжатию формы между прессующими поверхностями и давлению, развивающемуся внутри формы, стойкость к химическому действию резиновой смеси на металл формы и склонность смеси в большей или меньшей степени привариваться к форме.
Идеальный материал для изготовления форм должен обладать прочностью, твердостью, химической инертностью, хорошей теплопроводностью, удобством его обработки и низкой стоимостью. Основным материалом для изготовления форм является углеродистая сталь марок 30, 35 и 45, также применяются легированные стали. Устойчивая против коррозии хромоникелевая сталь особенно пригодна как материал форм для вулканизации изделий из хлоропреновых смесей. Изготовление форм из хромоникелевых сталей с применением последующей поверхностной закалки может значительно удлинить срок службы формового парка.
Для форм большого размера применение термической обработки ввиду возможности деформаций затруднительно; в таких случаях целесообразно производить электрическую поверхностную закалку. Хромирование вновь изготовленных стальных форм значительно повышает стойкость их в эксплуатации и обеспечивает гладкость поверхности изделий без применения смазки, но для форм с гнездами сложного очертания оно затруднительно. Трудность обработки стальных форм осложняет изготовление их, когда полость формы имеет особенно сложную конфигурацию. В этих случаях применяются формы, изготовляемые путем отливки под давлением из сплавов алюминия или путем так называемого уплотненного литья. Последний способ состоит в следующем: расплавленный металл, залитый обычным литейным способом в предварительно подогретую форму, подвергается в период кристаллизации прессованию на гидравлическом прессе. Применяемое при этом удельное давление составляет для алюминиевых сплавов МО7 Па.
По другому способу матрицы вдавливаются под нагрузкой 1,4—2,1-107 Па в налитый в изложницы и застывающий алюминий. Ценным качеством алюминия является его стойкость против действия серы и соединений, содержащих серу. Теплопроводность алюминия почти в 5 раз выше теплопроводности стали, что ведет к сокращению цикла вулканизации. Алюминий стоек к атмосферному воздействию, а потому хранение таких форм не требует особых условий; достаточно обычных складских сухих помещений. Стальные же формы, сохраняемые на складах, в целях предохранения от ржавления необходимо покрывать густой смазкой.
Конструкция вулканизационных форм должна обеспечить:
- быструю и удобную сборку и разборку формы, закладку заготовки, выемку вулканизованного изделия и очистку формы;
- возможность быстрого и полного заполнения полости формы резиновой смесью в период запрессовки и удаления при этом воздуха из полости формы, а также правильную конфигурацию и размеры изделия;
- прием выпрессовок и положение заусенцев (пленок) ни таких местах изделия, чтобы снятие их было наиболее удобно, с достаточным удалением их от рабочих кромок изделия.
Конструктивно следует различать три основных типа форм: открытые, закрытые или плунжерные и формы с литьевыми надставками. Примером открытых форм могут служить рамки для вулканизации различного вида клапанов, формы (рис. 25) для конических пробок аптечной и химической посуды и т. п. Для предупреждения растекания резины по плитам вулканизационного пресса формы сверху и снизу покрывают стальными листами. Заготовки помещаются в каждое гнездо формы; заусенцы выступают вверху и внизу изделия. К открытым формам могут быть отнесены плоские гравированные плитки для придания рифленого рисунка резиновым коврикам или матам различного вида и фасона, линейки для вулканизации некоторых видов ремней и лент.
Формы, в которых имеется только одна поверхность разъема (рис. 26), относятся также к типу открытых. Формы плунжерного типа выполняются таким образом, что нижняя часть крышки входит как плунжер в расширение полости формы (рис. 27), плотно замыкает ее и выпрессовывает заготовку в полость формы. Плунжерные формы дают возможность получать изделия с меньшим числом выходов заусенцев и применять упрощенные пластинные заготовки для многогнездных форм вместо индивидуальных заготовок на каждое гнездо. Плунжерные одногнездные формы обеспечивают заданное давление по контактной поверхности вулканизуемых изделий. Если конфигурация изделия может затруднить выемку его из формы, то средняя часть формы изготовляется составной из двух половин; эти разъемные части вкладываютея в наружную обойму формы (рис. 28). Если требуется обеспечить замкнутую полость в формуемом изделии, ТО форма снабжается соответственным сердечником, укрепляемым в деталях формы в требуемом положении.
Учитывая усадку резины при вулканизации, гнездо формы в горизонтальном направлении изготовляют несколько больших размеров в сравнении с размерами изделия, для которого форма назначается. По высоте гнездо формы с учетом выпрессовки увеличивают лишь в случае изготовления больших по высоте изделий. Объем заготовки должен быть несколько больше объема полости формы, чтобы можно было создать достаточное давление во время запрессовки. Излишек объема заготовки, выходящий в виде выпрессовки, приподнимая крышку формы, может повлечь за собой большее или меньшее изменение высоты изделия. Чтобы избежать связанного с этим искажения размеров изделия, формы по плоскости разъема снабжают канавками, расположенными концентрическими по отношению отверстия гнезда.
Радиус сечения канавок — 2 мм, а ширина фаски, отделяющей их от отверстия, 3 мм. В этих канавках и собирается вытесняемый из формы излишек заготовки резины. Для снижения толщины пленки (заусенцев) между обрезами гнезда и канавки формы в так называемых формах с режущей кромкой делают на верхней части формы небольшой выступ шириной 0,5—0,8 мм. Пленка в этом месте уменьшается до 0,2 мм и уже при выемке из формы изделие освобождается от выпрессовки и заусенцев. В формах с гнездами сложных конфигураций, имеющих несколько граней разъема, взамен одной кольцевой канавки иногда устраивают несколько пунктов приема выпрессовок, отделенных от изделия острыми режущими или очень узкими кромками. Расчленение выпрессовок ведет к отрыву их в момент выемки изделия из формы, но усложняет изготовление форм.
На рис. 29 показано изделие в момент нахождения в подобной форме с неснятыми заусенцами и выпрессовками.
Легкость и быстрота закрывания и разъема форм зависят от конструкции замка формы. В формах, изготовляемых токарной обработкой, замок составляют две конически обточенные соприкасающиеся детали. В формах прямоугольного очертания замок состоит из штифтов, находящихся на одной части формы, и соответствующих им втулок на другой ее части. Особое внимание должно быть обращено на обеспечение удобного выхода воздуха из полости формы. Следует предусматривать смыкание деталей формы в тех именно местах, где возможно скопление воздуха, при этом поверхность разъема должна, обеспечивая выход воздуха, затруднять выпресоовку резины.
На рис. 30 даны разрезы гнезда формы неудовлетворительной и хорошей конструкций для уплотнительных колец к гайкам пожарных рукавов (рис. 31). Вследствие возможности свободного выхода резины при запрессовке в форме по рис. 30, а наблюдается утечка резины, приводящая к недопрессовке изделия. Изменение замка формы, приведенное на рис. 30, б, обеспечивает плотное закрытие формы, не допускающее утечку резины. В отдельных случаях для выхода воздуха целесообразно просверливать небольшое отверстие в нижней части формы. Получающийся на конце изделия небольшой отросток резины удаляется последующей операцией отделки.
Применение литья под давлением привело к видоизменению вулканизационных форм путем высверливания двух или нескольких литьевых каналов в крышке формы. Для одногнездных форм весьма удобно иметь одну такую «литьевую крышку», закрывая наполненные резиновой смесью формы их обычными крышками. Дальнейшая разработка метода литья под давлением привела к формам с литьевыми надставками. В верхней крышке такой формы закрытого типа (рис. 32) растачивается литьевой цилиндр с литьевым отверстием в дне. Помещенная в этот цилиндр дозированная закладка резиновой смеси продавливается в полость формы специальной плунжерной крышкой формы. Точная дозировка закладки дает изделие правильной высоты при малой выпрессовке. Применение таких форм — один из путей к организации поточного производства на автоматизированных линиях. В плунжерных литьевых формах (рис. 32) можно изготовлять также изделия больших размеров и сложных очертаний.
Очистка форм. Безукоризненная чистота форм — основное средство предупреждения приваривания к ним изделий. Если от смазок и опудривающих материалов образовались хотя бы небольшие налеты, их следует незамедлительно удалить протиркой гнезд формы. При образовании устойчивой пленки нагара форму следует передавать в чистку. Нагар не только загрязняет поверхность изделий, но, снижая теплопроводность формы, может повести к не довулканизации изделий. Очистку стальных и алюминиевых форм производят с помощью металлических щеток, укрепляемых в патроне гибкого вала, приводимого в движение от электромотора. Более производительна очистка пескоструйным прибором с применением мелкого песка, молотой скорлупы орехов или иного нестойкого абразива. Однако очистка с помощью механических средств неизбежно связана с разработкой гнезд формы. Поэтому более целесообразно производить химическую очистку стальных форм в горячем растворе щелочи. Формы погружают на 3—10 ч в горячий 15—20% раствор NaOH, обогрев ванны производится глухим паром.
Щелочная очистка значительно ускоряется, если через ванну пропускать постоянный ток. Формы подвешивают на аноде, но через каждые 3 мин меняют направление тока. После электролитической очистки форм следует проводить 2—3-минутную обработку их 5% раствором НС1 с последующей смывкой, нейтрализацией и сушкой. Способы химической и электрохимической очистки достаточно просты и недороги, но мало применимы при очень загрязненных формах, поэтому очистку последних следует производить своевременно. Есть основания полагать, что для очистки форм найдут применение генераторы ультразвука.
Расчет на прочность деталей вулканизационных форм. Резиновая смесь при отливке и вулканизации оказывает значительное давление на стенки деталей вулканизационных форм. Удельное давление при отливке достигает (4,3—4,5) • 107 Па, а при вулканизации — до 8,0-107 Па. В соответствии с этим должны быть рассчитаны минимальные размеры стенок форм, обеспечивающих при малой массе и габаритах форм достаточную прочность. Е. Г. Копаневич приводит основы расчета на прочность деталей форм по опыту производства пластмасс. Приводимые им примеры имеют значение и для расчета вулканизационных форм производства РТИ. Расчет стенок вулканизационных рамок. Кольцевые вулканизационные рамки (рис. 33), а также детали форм с цилиндрическими полостями должны быть рассчитаны на прочность стенки. Расчет допустимого напряжения производят по уравнению Ламе по теории наибольших нормальных напряжений
Уравнение (1.2) не учитывает осевое нагружение рамки со стороны плит вулканизационного пресса. Однако эта нагрузка скажется лишь некоторым увеличением запаса прочности круглой рамки. Допустимое напряжение на разрыв Rz для закаленной стали принимают равным 9,0 кН/см2, а для не закаленной стали 20 равным 4,0 кН/см2. Расчет стенок круглых и прямоугольных обойм. В ряде случаев детали форм помещаются в обойму (как это показано на рис.28). Напряжение на разрыв стенки обоймы определяется следующим уравнением