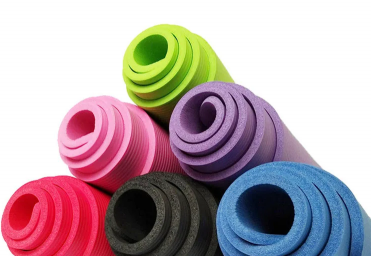
Бутадиен-нитрильные каучуки (БНК) это каучуки специального назначения. БНК является продуктом сополимеризации бутадиена и нитрила акриловой кислоты. Полимеризация проводится в водной эмульсии. Меняя соотношение компонентов, можно существенно изменять свойства получаемых полимеров. Полимеризация может осуществляться как при высоких, так и при низких температурах.
В товарных каучуках, кроме полимера, допускается небольшое содержание минеральных веществ, определяемых в виде золы (не более 1% вместе с опудривающими веществами) и летучих (не более 1%). Каучуки при получении заправляются окрашивающими (2-3% фенил-β-нафтиламин) или неокрашивающими (1,2-2% алкилзамещенные бисфенолы) противостарителями.
Макромолекула сополимера построена из статистически чередующихся звеньев бутадиена и нитрила акриловой кислоты (НАК).
Звенья бутадиена, присоединенные в положение 1,4, имеют преимущественно транс-конфигурацию; содержание звеньев бутадиена, присоединенных в положении 1,2, не превышает 10% и уменьшается с увеличением содержания присоединенного НАК.
Среднемассовая М БНК составляет 100-300 тыс. при широком ММР. Эти каучуки аморфны и не кристаллизуются ни при хранении, ни при растяжении
В России выпускают полимеры с низким (17-20%), средним (27-30%), высоким (36-40%) и очень высоким (50%) содержанием НАК, которые соответственно обозначают: СКН-18, СКН-26, СКН-40, СКН-50. К обозначению каучука, заправленного неокрашивающим противостарителем, добавляется буква Н, например СКН-18Н.
Физические свойства.
Физические свойства БНК существенно зависят от содержания НАК:
БНК хорошо растворяются в кетонах, ароматических и хлорированных углеводородах, сложных эфирах и очень плохо-в алифатических углеводородах и спиртах.
С увеличением содержания в полимере связанного в НАК существенно увеличивается межмолекулярное взаимодействие между цепями полимера и плотность, повышается температура стеклования, снижаются диэлектрические свойства, уменьшается растворимость в ароматических растворителях и увеличивается стойкость к набуханию а алифатичеких углеводородах.
Технологические свойства
Вязкость по Муни (100°С) отечественных каучуков составляет 50-70 или 90-130 (соответственно «мягкие» и «жесткие» каучуки). Для большинства типов зарубежных каучуков и их композиций с ПВХ этот показатель лежит в пределах 40-90. Перерабатывают БНК на обычном оборудовании резиновых заводов (вальцах, смесителях, каландрах, экструдерах), изделия вулканизуют при 140-160°С в прессах, котлах и других. «Жесткие» каучуки перед введением в них ингредиентов пластицируют.
БНК технологически совместимы с другими каучуками, например бутадиеновыми, бутадиен-стирольными, полисульфидными, а также с феноло-формальдегидными смолами и др. Для их вулканизации применяют серу, тетраметилтиурамдисулъфид (при получении теплостойких резин); ускорителями вулканизации служат, как правило, N-циклогексилбензотиазол-2-сульфенамид (сульфенамид Ц), ди (2-бензотиазолилдисульфид), 2-меркаптобензотиазол. В качестве наполнителей резиновых смесей используют технический углерод (сажу), мел, каолин, SiO2 и другие, в качестве пластификаторов — главным образом сложные эфиры (фталаты, себацинаты), а также канифоль, инден-кумароновые и феноло-формальдегидные смолы. Общее содержание ингредиентов может изменяться в пределах 50-150 мас. ч. на 100 мас. ч. каучука.
В настоящее время значительные количества БНК выпускаются с использованием биологическиразлагаемых парафинатных или канифолевых эмульгаторов с последующим выделением из латекса при помощи солей кальция. Такие каучуки обозначаются БНКС. Они имеют в своем составе до 5% некаучуковых компонентов.
Обрабатываемость каучуков различных марок зависит от их исходной вязкости, а так же от содержания нитрильных групп. Для всех каучуков жестких типов необходима предварительная пластикация, причем наиболее эффективна пластикация на вальцах при температурах 30-40ºС.
Каучук, полученные низкотемпературной полимеризацией, имеют лучшие технологические свойства, по сравнению с каучуками «горячей» полимеризации. Переработка мягких каучуков не вызывает принципиальных трудностей.
Свойства вулканизатов
Наиболее важное свойство резин на основе БНК — стойкость к действию агрессивных сред (бензина, керосина, мазута, смазочных масел, растительных и животных жиров, а также глицерина, этиленгликоля, формальдегида, морской воды, разб. H2SO4 и НС1). Резины, содержащие активные наполнители, характеризуются высокими прочностными свойствами, износостойкостью, сопротивлением тепловому старению. Бензо- и маслостойкость резин, а также многие другие их свойства улучшаются с увеличением содержания в БНК акрилонитрильных звеньев. При гидрировании БНК резко возрастает теплостойкость резин.
Вулканизаты пригодны для эксплуатации при температурах до 120-130°С, а полученные на основе каучуков специальных типов с применением CdO в качестве активатора вулканизации — до 150-160 °С
Газо- и водопроницаемость резин из БНК значительно ниже, чем резин из неполярных каучуков (изопреновых, бутадиеновых, бутадиен-стирольных). Газопроницаемость тем меньше, чем больше содержание в каучуке акрилонитрильных звеньев, например, коэффициент газопроницаемости [в м2/(Па*с); 25°С] ненаполненных вулканизатов БНК с содержанием акрилонитрильных звеньев 27 и 39% составляют соответственно 2,9*10-17 и 0,73*10-17 (О2), 0,81*10-17 и 0,18*10-17 (N2), 23,5*10-17 и 5,6*10-17 (СО2).
По теплофизическим свойствам резины из БНК практически равноценны резинам из других каучуков: их коэффициент объемного расширения (4-6)*10-4 К-1, коэффициент теплопроводности 0,25-0,40 Вт/(м*К), удельная теплоемкость ~ 2 кДж/(кг*К). Присутствие в макромолекуле каучука полярных нитрильных групп обусловливает сравнительно высокую электрическую проводимость резин, резко возрастающую с увеличением содержания акрилонитрильных звеньев; например, для ненаполненных резин на основе каучуков с 17-20 и 36-40% этих звеньев составляет соответственно 650 и 10 МОм-м.
БНК и резины на их основе относятся к сгораемым материалам со сравнительно низким кислородным индексом: для каучуков он не превышает 0,2, для резин составляет 0,2-0,3.
Одним из существенных преимуществ резин на основе БНК по сравнению с резинами на основе НК, СКИ-З, СКС-30 является их более высокая стойкость к тепловому старению, что объясняется образованием при окислении промежуточных продуктов, являющихся ингибиторами старения.
Резины на основе БНК имеют хорошую адгезию к латунированному металлу и приближаются в этом отношении к резинам из НК. Прочность крепления их к алюминию и его сплавам, стали, чугуну, латуни, цинку, бронзе выше прочности самого вулканизата.
Получение каучуков, их модификации
БНК синтезируют радикальной сополимеризацией мономеров в водной эмульсии при 5°С («холодная полимеризация») или 30°С («горячая полимеризация») в присутствии эмульгатора, например алкилсульфоната Na или Na-соли дибутилнафталинсульфокислоты, и регулятора молекулярной массы, например трет-додецилмеркаптана или диизопропилксантогендисульфида. В качестве инициатора полимеризации применяют окислительно-восстановительную систему, например K2S2O8 и триэтаноламин. Степень превращения мономеров составляет обычно 70-80%. После обрыва полимеризации (например, при помощи гидрохинона), введения в латекс антиоксидантов и отгонки непрореагировавших мономеров каучук коагулируют, промывают водой и сушат. Цвет БНК от светло-желтого до темно-коричневого; содержание в них примесей (остатков эмульгаторов, влаги и др.) до 5%. Выпускные формы — брикеты, смотанная в рулоны лента, пластины, листы, крошка, гранулы, порошки.
В промышленных масштабах выпускают композиции БНК с ПВХ (обычно в соотношении 70:30 или 50:50), на основе которых получают озоно-, износо- и огнестойкие изделия. Существуют также другие разновидности этих каучуков: жидкие; пластифицированные диоктилфталатом; с невымываемым антиоксидантом сильно структурированные сополимеры бутадиена, акрилонитрила и 1-2% дивинилбензола; содержащие в макромолекуле 1,5-5% звеньев метакриловой кислоты. К нитрильным каучукам относят также выпускаемые в промышленности сополимеры изопрена с акрилонитрилом, тройные сополимеры бутадиена, акрилонитрила и 2-циан-этилметакрилата, а также высоконасыщенный гидрированный нитрильный эластомер. Описаны сополимеры с регулярно чередующимися звеньями бутадиена и акрилонитрила (так называемые альтернантные, или чередующиеся каучуки), которые получают каталитической сополимеризацией в растворе или суспензии.
Так как БНК не кристаллизуются при деформации, ненаполненные резины на их основе характеризуются низкими прочностными показателями и практического значения не имеют.
Компоненты эмульсионной полимеризации.
Дисперсионная среда. Дисперсионная среда не должна вступать в химическое взаимодействие с мономером. Чаще всего для этих целей применяют воду, к которой применяются особые требования по чистоте. Вода не должна содержать солей железа, кальция и других двухвалентных металлов. Первоначально в качестве дисперсионной среды использовали дорогостоящий паровой конденсат или дистиллированную воду. Позднее в промышленности перешли на деионизированную или умягченную цеолитом воду. Для удаления следов растворенного кислорода воду иногда подвергают деаэрации под вакуумом.
Соотношение фаз. Дисперсионная фаза при эмульсионной полимеризации состоит обычно из одного мономера или смеси мономеров. Соотношение дисперсионной среды и дисперсной фазы при ЭП колеблется в довольно широких пределах: от 100 до250 мас. ч. дисперсионной среды на 100 мас.ч. дисперсной фазы. Это соотношение определяется условием проведения процесса и назначением получаемого латекса. Обычно при высокотемпературной полимеризации и в случаях, когда требуется получение высококонцентрированного латекса, соотношение дисперсионной среды и дисперсной фазы составляет 105:100 или 100:100, меньшее количество дисперсионной среды создает дополнительные трудности ввиду повышения вязкости системы. Кроме того, с уменьшением количества дисперсной фазы ухудшается качество полимера, так как возрастает роль реакций переноса цепи через полимер. Поэтому ЭП при соотношении фаз ниже 100:100 проводят редко.
Осуществление полимеризации при низких температурах ( 5ºС) в условиях повышенной вязкости реакционной среды заставляет увеличивать соотношение дисперсионной среды и дисперсной фазы. Для улучшения условий теплообмена и обеспечения плавного и регулярного управления процессом в промышленности применяют соотношение дисперсионной среды и дисперсной фазы (250-200):100. Такое большое количество воды в эмульсионной системе, хотя и положительно сказывается на ходе процесса полимеризации и свойствах получаемого каучука, но приводит к неэффективному использованию оборудования. Уменьшение соотношения до (150-135):100 позволяет увеличить съем каучука с 1м³ реактора и снизить расход материалов при выделении каучука из латекса, но несколько замедляет процесс, снижает агрегативную устойчивость латекса и ухудшает технологические свойства каучука.
В настоящее время сополимеризацию проводят при большом избытке ( в 2-2,5 раза) дисперсионной среды.
Эмульгаторы. Обязательным компонентом при ЭП является эмульгатор, назначение которого состоит в увеличении устойчивости эмульсии мономеров в воде и стабилизации коллоидной дисперсии образующегося полимера. Изучение механизма ЭП выявило большую роль эмульгатора в процессах образования и дальнейшего роста макромолекул. Как правило, с увеличением концентрации эмульгатора в водной фазе скорость полимеризации существенно возрастает.
Основную группу промышленных эмульгаторов составляют анионоактивные эмульгаторы типа мыл или солей сульфокислот, например натриевые соли алкилсульфонатов общей формулы СnН2n+1С6Н4SO3Na. Распространены соли стеариновой, олеиновой и пальмитиновой кислот, синтетических жирных кислот фракции С10-С16, кислот канифоли. Из солей сульфокислот применяются различные некали. Некаль широко применяли в промышленности синтетического каучука, однако постепенно он вытеснен из производства другими эмульгаторами.
Успешно применяются в качестве эмульгатора канифолевое мыло, которое по сравнению с некалем имеет ряд преимуществ:
1. При коагуляции латекса смоляные кислоты канифоли почти целиком остаются в каучуке, увеличивая его выход, получаемые сточные воды почти не содержат мыла, и их очистка не вызывает затруднений.
2. Несколько улучшаются технические свойства каучуков, получаемых с использованием канифолевых эмульгаторов, в частности возрастает клейкость сырых резиновых смесей, увеличиваются условная прочность при растяжении, сопротивление раздиру и истиранию.
В отечественной и зарубежной промышленности используются в качестве эмульгаторов натриевые и калиевые соли диспропорционированной канифоли, называемые дрезинатами.
Природа катиона мыла (калий или натрий) не влияет на скорость ЭП и ММР каучука. Вулканизаты эластомеров, полученных с натриевыми мылами как гидрированной, так и диспропорционированной канифоли, имеют более низкие значения условной прочности при растяжении по сравнению с вулканизатами каучуков, полученных с калиевыми мылами канифоли.
Канифолевые эмульгаторы можно применять совместно с эмульгаторами на основе синтетических жирных кислот. Мыла синтетических жирных кислот, называемые парафинатными эмульгаторами, используются в производстве ряда каучуков, в том числе бутадиен-метилстирольного и бутадиен-нитрильных сополимеров. Парафинатные эмульгаторы ускоряют процесс полимеризации, в результате чего происходит перераспределение частиц по размерам и снижение устойчивости латекса. Чтобы поддержать в системе необходимую величину поверхностного натяжения, вводятся электролиты ( хлорид калия, тринатрийфосфат).
Парафиновые эмульгаторы наиболее эффективны в производстве БНК, так как при их применении сополимеризация протекает с максимальной скоростью.
При выделении каучука из латекса, полученного с использованием парафинатного эмульгатора, большая часть жирных кислот остается в каучуке. Вулканизаты таких каучуков обладают пониженными физико-механическими показателями.
В качестве дополнительного стабилизатора, повышающего устойчивость латекса, чаще всего используется лейканол-натриевая или калиевая соль продукта конденсации в-нафталинсульфокислоты с формальдегидом.
Инициаторы и активаторы. Полимеризация при высоких температурах (48-50ºС) протекает достаточно эффективно при использовании в качестве инициаторов водорастворимых персульфатов (К2S2O8 или (NH4)2S2O8). Наиболее активным инициатором этого типа является персульфат аммония, что связано, по- видимому, с восстановительными свойствами аммиака, образующего окислительно- восстановительную систему с персульфат- ионами. Но в промышленности применяется главным образом стабильный при хранении персульфат калия.
Низкотемпературная полимеризация (5ºС) требует более эффективных инициаторов. Первоначально для этих целей применяли необратимую ОВ систему, состоящую из гидропероксида изопропилбензола и пирофосфата двухвалентного железа. В дальнейшем в эту систему начали вводить дополнительный восстановитель (глюкозу) для перевода трехвалентно железа в двухвалентное.
В 1961 году впервые была применена в отечественном производстве для синтеза каучука обратимая ОВ система, состоящая из гидропероксида изопропилбензола, солей двухвалентного железа и ронгалита. В настоящее время- это основная система инициирования низкотемпературной полимеризации в эмульсии.
В щелочной среде ионы железа не существуют, поскольку образуется нерастворимая гидроокись. Поэтому в систему вводят двунатриевую соль этилендиаминтетрауксусной кислоты ( трилон Б), которая при взаимодействии с сульфатом железа (II) дает хорошо растворимый в воде комплекс.
В водной среде комплекс трилона Б с двухвалентным железом вступает в ОВР с гидропероксидом изопропилбензола, сопровождающуюся образованием свободных радикалов и превращением железа (II) в железо (III).
С увеличением концентрации гидропероксида изопропилбензола и ионов двухвалентного железа и повышением температуры возрастает скорость полимеризации.
Для восстановления трехвалентного железа в двухвалентное используется ронгалит.
Кроме этой основной реакции ронгалит может расходоваться не взаимодействие с применяемым гидропероксидом. Скорость этой реакции существенно зависит от рН среды и температуры. В кислой среде даже при температурах от 0 до 5 ºС примерно 20-25% ронгалита вступает во взаимодействие с гидропероксидом, тогда как в щелочной среде даже при 30ºС эта реакция протекает с незначительной скоростью. Поэтому важно для эффективного действия данной обратимой ОВ системы поддерживать в водной среде постоянное оптимальное значение рН. Для этой цели применяются специальные буферные вещества ( напимер, тринатрийфосфат).
Регуляторы молекулярной массы. Для получения каучуков с определенной молекулярной массой используется реакция переноса цепи через регулятор длины цепи; варьируя количество и тип регулятора можно получать каучуки с различными значениями молекулярной массы. Чаще всего в качестве регуляторов в промышленности СК применяются алифатические меркаптаны, реже- диизопропилксантогендисульфид (дипроксид). Обычно меркаптаны вводятся в систему в один прием, тогда как дипроксид необходимо дозировать дробно с обязательным введением части его в момент возможного образования геля (степень превращения мономеров 30-35%).
Прерыватели (стопперы) полимеризации. В большинстве случаев ЭП обрывают при достижении степени превращения 58-62% так как при дальнейшем увеличении степени превращения скорость полимеризации снижается и возрастает роль реакций переноса цепи через полимер, что приводит к существенному ухудшению технологических свойств каучука. Для обрыва цепи полимеризации используют соединения, являющиеся типичными ингибиторами радикальных процессов. В промышленности СК в качестве стопперов применяют древесно- смоляной антиполимеризатор, содержащий около 65% фенолов, гидрохинон, n- оксидифениламин, диметилдитиокарбамат натрия.
Применение
Благодаря высокой стойкости к действия масел и других агрессивных агентов БНК нашли широкое применение для изготовления различных маслобензостойких РТИ – прокладок, рукавов, сальников, бензотары и др., а так же для производства изоляционных и электропроводящих резин, клеев и эбонитов, покрытий, стойких в агрессивных средах. Каучуки с нетоксичным, неокрашивающим стабилизатором употребляются для изготовления маслостойких резиновых деталей доильных аппаратов и других изделий пищевого машиностроения.